Editors Note: This is a guest post by Ethan Hagan from One Project Closer. Check out some of his other manly contributions to AoM like repairing drywall and building a workbench.
As I continue to expand my workshop, I quickly discovered the need for some good sawhorses. Sawhorses are great for setting up a temporary workspace, out-feed (on my table saw), and more. Now you can slap some sawhorses together pretty quickly and they’ll work just fine; Brett shared a fast and easy sawhorse design awhile back if you’re looking for something nice and simple. But I didn’t want to compromise on features. So I scoured the internet for ideas, and eventually decided on this design called the Shopdog.
These are not the easiest sawhorses to build. However, they are extremely strong, durable, collapsible and versatile. The versatility comes from the fact that the cross member can be modified depending on the application. For instance, cutting V notches into the top makes it easy to support round pipe. Stapling carpet over the top is perfect for protecting woodworking projects. Best of all, if the cross member gets messed up, all you have to do is swap in a new piece of 2×4. I’m confident that you won’t find a better workshop sawhorse anywhere else. Now here’s how to build ’em.
Tools & Materials List
These are the tools and materials I used to build the sawhorses. The total cost for each sawhorse is less than $20, and a big chunk of that is for the locking tie-down. If you can find a suitable alternative, I’ll bet you can get the price tag under $15 which is cheaper than most of what you’ll find at the Big Box stores!
The Shopping List
- (3) 8 foot 2×4’s
- (2) 3/8″ x 3-1/2″ carriage bolts
- (6) 3/8″ washers
- (2) 3/8″ nuts
- (10) 2-1/2″ wood screws
- (1) 6′ locking tie-down
Tools
- Compound miter saw (must be capable of bevel and miter cuts)
- Jigsaw (or handsaw)
- Drill/driver
- Square
Step 1: Cut the Lumber for Individual Components
To keep these instructions as clear as possible, I’ve labeled a couple of pictures and listed the necessary cuts. Remember that you’ll need to cut miter and bevel angles on the top and bottom of each piece while maintaining a consistent length. All my legs measure 40″ long, but you can change that to whatever length you prefer.
The cuts I list below assume the work piece is on the right-hand side of the miter saw, same-side up.
- Leg 1 & 3 Top: 25° miter right, 10° bevel right
- Leg 1 & 3 Bottom: 25° miter right, 10° bevel left
- Leg 2 & 4 Top: 25° miter left, 10° bevel right
- Leg 2 & 4 Bottom: 25° miter left, 10° bevel left
- Lower Supports: 32″ and 28″ long with 10° miter cuts on both sides
- Upper Support: 24-1/2″ long with 10° miter cuts on both sides
- Cross Member: 36″ long, straight cut on both sides.
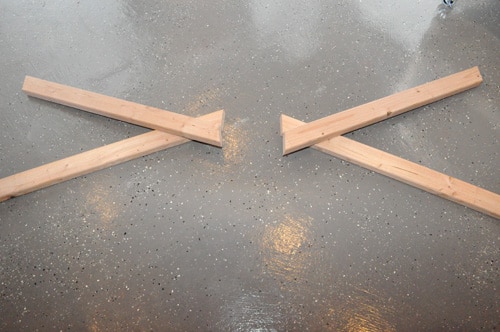
Once the legs are cut, they should look like this.
Step 2: Cut the Notch
The cross-member needs to sit parallel to the ground (for optimal support), and that requires making a compound cut to notch each leg. Unfortunately, you can’t complete the notch with just a miter saw, and here’s where the jigsaw come into play. If you’re looking closely, you’ll notice the cross member sits proud (higher than the legs) and this is because that little extra space helps protect the legs from saw blades.
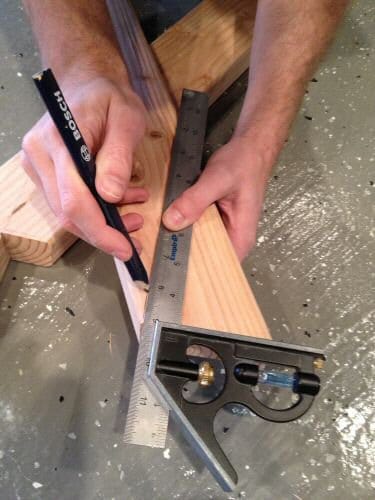
First, mark your cut on the “inside” of each leg. The first line will be straight down and perpendicular to the top edge. Mark the line by setting your square on the top of the leg and scribe a line starting at the corner. This line should measure 3-1/8″ (just shy of the actual height of a 2×4).
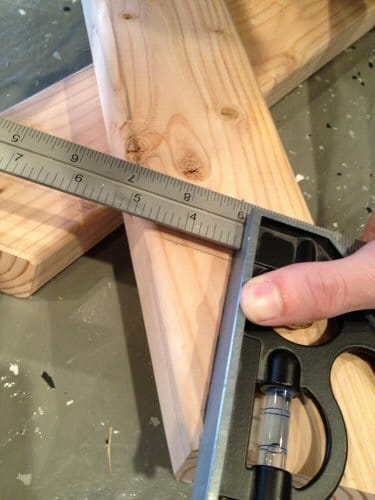
The next line is perpendicular and will continue all the way to the edge of the 2×4. It should measure 1-1/2″ long.
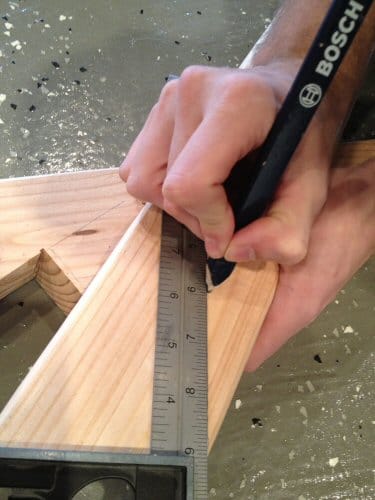
Flip the leg over and repeat the process.
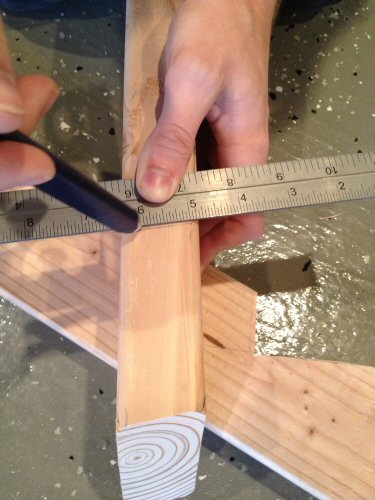
Next, turn the 2×4 on end and draw a straight line between the two sets of markings. It’ll be angled at 10° which matches the top.
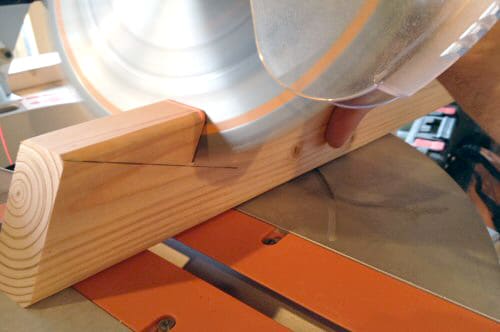
You can make the first cut with your miter saw set to a 25° bevel and 10° miter. Be careful as the depth of this cut is different on each side and you don’t want to cut too deep.
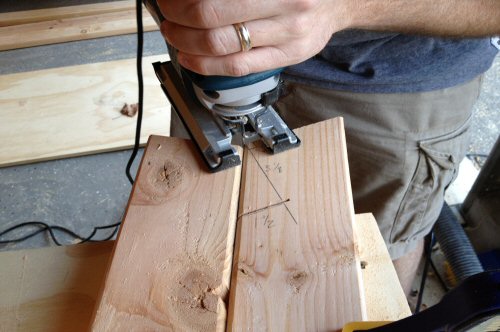
The second cut needs to be done with a jigsaw, and I used some scrap for additional support. Again, be careful because the depth is different on either side, and you’ll need to angle the saw to complete the cut.
Notch all four legs on their inside edge using the same technique.
Step 3: Drill Bolt Holes
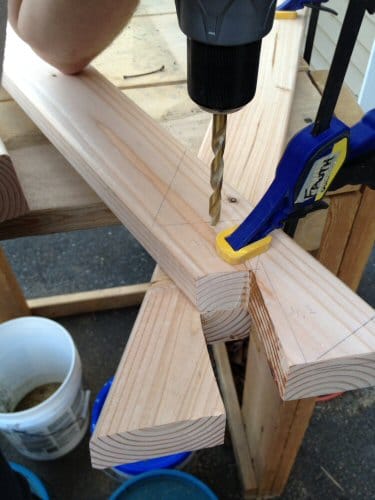
Next, you need to drill a hole for the carriage bolt which acts as a hinge to collapse the sawhorse. Drill the hole 6″ down, centered on the 2×4. I found it easiest to drill through both legs at the same time. In order to position the legs correctly, put a piece of scrap 2×4 in the notch.
Step 4: Insert the Carriage Bolts and Washers
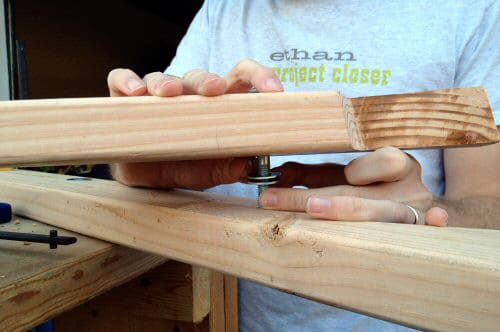
Slide the carriage bolts through with two washers in-between the legs to allow them swing. Put on a third washer next to the nut, and tighten it (but not too tight).
Step 5: Attach Cross Supports Using Wood Screws
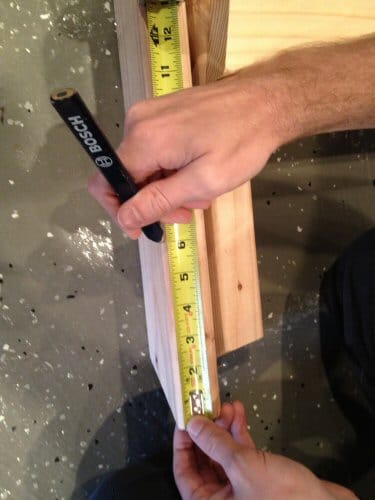
Now it’s time to attach the three support pieces. I suggest drilling pilot holes to avoid splitting the wood since the screws are so close to the end grain. I placed the lower support 6″ up the leg and the upper support about the same distance down from the top.
Step 6: Install the Strap
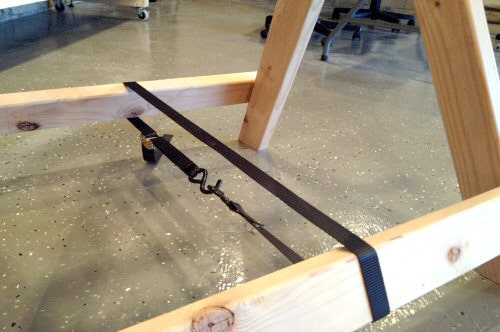
To firmly sandwich the cross member between the legs, use a locking strap (or ratcheting strap) to pull the legs tight.
Final Thoughts and Pictures
I’ve been using these sawhorses since January, and I love ’em! Like I said, they’re not the easiest to build, but they’re worth it.
____________________________
Ethan Hagan is the primary editor at One Project Closer. Ethan spends most of his days shadowing real contractors on actual job sites and most of his nights writing about the experience. To see what I mean, check out their expert guides like How to Build a Shed Ramp and How to Solder Copper Pipe. If learning and interacting with pro contractors sounds like something you’d enjoy, sign up for OPC email updates.